Our client, a large copper mine in Australia, determined that output for a particular level of operational expenditure could be materially improved by focusing on Direct Labour.
Results
Achieved an annual reduction in unproductive time equivalent to over $1 Million
Tools
The tools being used for this case study are as follow duis aute irure dolor in reprehenderit in voluptate.
-
APC Pyrite
-
On-personnel tags and
readers -
IP infrastructure
-
Visualisation Screens
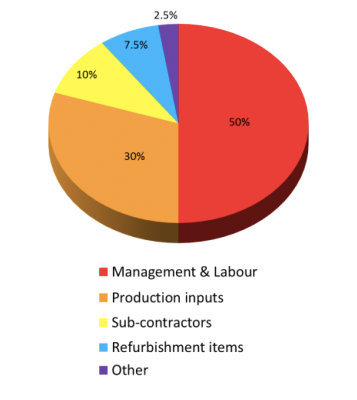
As this component of Opex represented half of the total, by making small improvements in effective work time, significant additional productivity could be achieved. This would translate into higher output and copper produced.
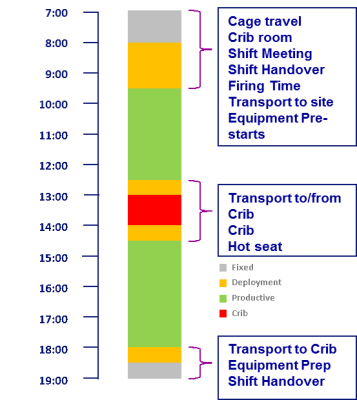
APC identified gaps in productive effort, and worked with the supervisors to reduce those gaps over time. As seen in the diagram, some of those gaps are fixed, others can be reduced or eliminated.
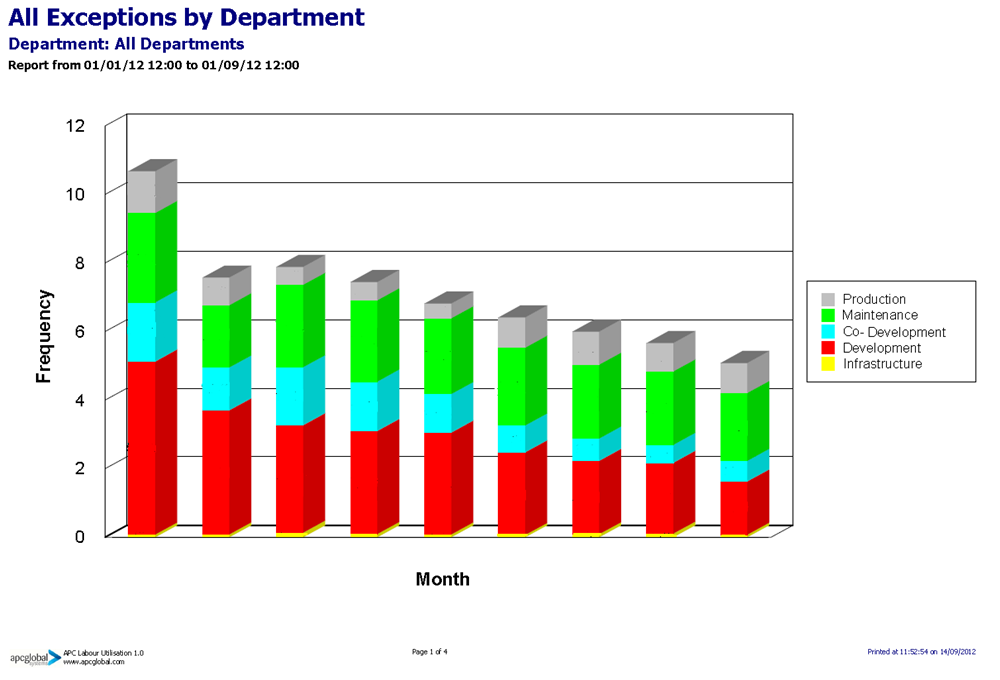
By identifying acceptable limits to the time taken to reach the workplace, after firing or at shift start, as well as identifying early leavers from the shift, exceptions to desired behaviour are collated. Initially, the number of exceptions was high, but soon after deployment of APC Pyrite, exceptions quickly dropped. From then, the reduction in exceptions was slower, but still noticeable – as shown in the chart, which breaks the shift down into teams.
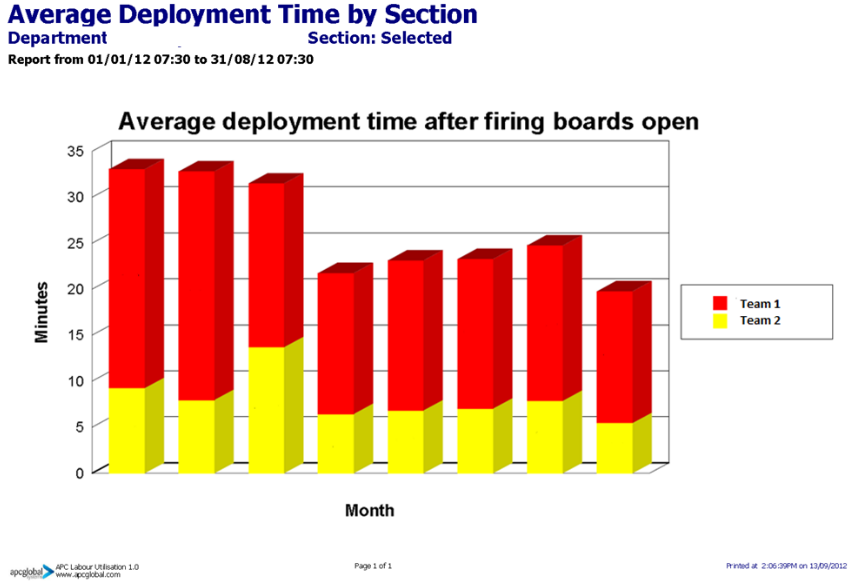
As average deployment time to the workplace continued to decrease, it was clear that unproductive time decreased, and a value was put on that at $1 per minute. In this case, the average time decreased by 13 minutes. For a 40-man crew on day and night shift, with 300 work days per year this translated to $312,000 per annum. This actually manifested itself as an increase in drilled metres, per unit of labour input.
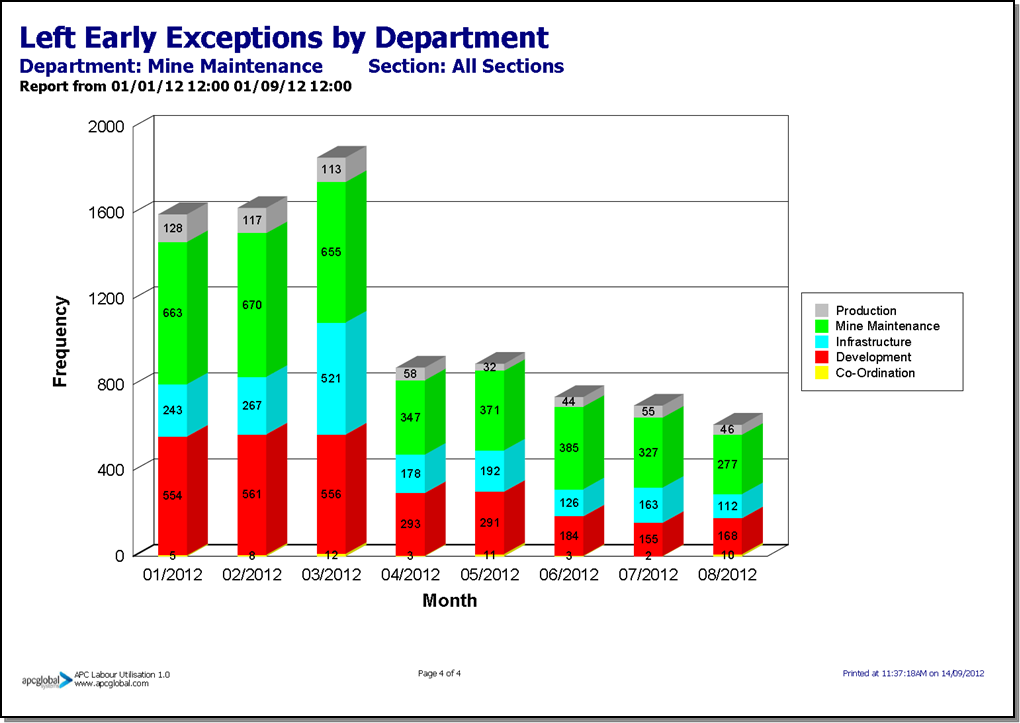
Early finisher performance
The number of people who left the shift early decreased from 1593 in January, to 742 in June. The average early leaver left 15 minutes before he should have.
Over the evaluation period, on average there were 1000 fewer early leavers per month. Again, with each minute of productive time lost worth $1, this equates to $180,000 pa.
In summary, the benefits to this mine came through three areas:
- Cultural change: Reduction in exceptions by 30% shows behavioural change resulting in more time on the job
- Deployment savings
More time is spent on the job through faster deployment after firing.
The annual wasted time saving for all departments is:
600 crew x 5 minutes x 300 Days x $1 = $900,000 pa reduction in non-value added time - Early finish savings
The annual wasted time saving for all departments is:
1000 exceptions x 15 minutes x 12 Months x $1 = $180,000 pa reduction
Project Benefit (Year 1)
$900,000 deployment + $180,000 early finish = $1,080,000